
THIN FILM EVAPORATORS
Thin Film Evaporation (WF TFE)
Wiped Film Evaporator (WFE) is an approach to distillation that creates a consistent “thin film” of material along the evaporative surface, maximizing surface area and heat transfer. Grooved wipers or rollers (in PTFE or PBI) are held in a basket spun by an overhead motor. During operation, crude oil is displaced evenly as it presses the heated surface of the jacketed body. The idea is to create the optimum conditions for heat transfer and evaporation so that fine separations and low temperatures distillations are possible.
Sensitive Distillations
Distillations often require temperatures high enough to damage to the target itself or other valuable compounds in the crude feed. However, under rough & fine vacuum (reduced vapor pressure), the boiling points are greatly reduced. This is combined with a short retention time as your feed runs down the evaporative wall. Operators are then able to avoid thermal decomposition of their product(s) and often enjoy a significant increase in productivity. The wiping mechanism and thin film principle ensures energy is being used efficiently.
Why a TFE?
What distinguishes this distillation approach is its external condenser. These systems are designed for multiple solvent separations, bulk recovery of solvents or the removal of residual solvent (<100ppm).
Due to the even, thin distribution of material during distillation, TFE is considered best practices for driving down distillable PPM impurities in bulk liquids. With that, the orientation of the external condenser plays a role in the optimization of the specific process.
Thin Film Evaporators are ideal for distillations that are sensitive to heat, high in viscosity and/or molecular weight. And, bench systems predictably scale-up into fully continuous pilot/kilo skids.
Minimum thermal decomposition.
High evaporation efficiency.
Uniform thin film.
Uniform heat distribution.
Process visibility.
Greaseless valves, joints & bearing.
cGMP distillation of residual solvents <100ppm
Up to 230C jacket temperatures.
Easy connection to auxiliary equipment
Consistent evaporative performance.
A1-CTFE Local Showers Series
The APICAL A1-CTFE Local Showers series consists of continuous, glass thin film wiped film evaporators with external condenser designed for compliant processing of solvents and light molecular weight compounds into high-purity distillates under deep vacuum conditions. Operators enjoy the precise control, high efficiency solvent recovery and throughput while owners rely on the durability, product consistency and protection against contamination Apical systems offer.
Intended to perform low temperature distillations and near boiling point separations —ideal for difficult and sensitive purifications.
Sizes from .025m² to 5m² wiped surface area in glass
Throughputs (water) from 250mL/hour to over 200,000mL/hour, offering a solution to bulk & residual needs at-scale.
Depending on the orientation of the external condenser, these systems are designed for bulk light distillation or precise control of residual light-weight content. This method’s reticulate is a heavy weight product that has been relieved of its residual solvent content or light-weight components down to minimum amounts.
Thin film evaporation is considered best practices for the removal & separation of solvents in pharmaceutical production and can separate temperature-sensitive aromas with limited degradation within the food & perfume science realm.
And, with Apical systems being built to c/EU-GMP and FDA standards, we remain conscious of OSHA safety guidelines. Apical ensures the safety of your operators with the addition of insulation, warning labels, low pressure heat transfer fluids, shielding and comprehensive training.
Apical has taken years of validated field experience and product trials to develop practical technologies that work every day. We combine academic principles with cutting-edge design to provide equipment that can be relied on for years to come with safe, easy operation, high throughputs and consistent product.
The APICAL A1-CTFE Local Showers is composed of a range of wiped surface areas; .25m², .1m², .35m², .5m², 1m², 2.5m², 5m². All ancillary glassware, motors, temperature control and pumps scale appropriately.
These systems utilize large tubing to ensure an unimpeded vapor path which is critical to maintaining deep vacuum at the process rather than just at the pump. With that, the external condenser is orientated and sized to carry the full capacity of distilled under the increased efficiency these deeper vacuum conditions allow.
Scaling these dimensions appropriately is one of the keys to high throughputs, low residual solvents and efficient commercialization.
No myths about residence time, degradation or physics, no designs with built-in obsolescence, no exaggerations about system capabilities or pay-to-play obstacles to efficient processing.
Apical has tested a wide range of designs under production settings to pierce the veil and remove the mystique around botanical distillations so business operators can focus on the customer and not a daily headache.
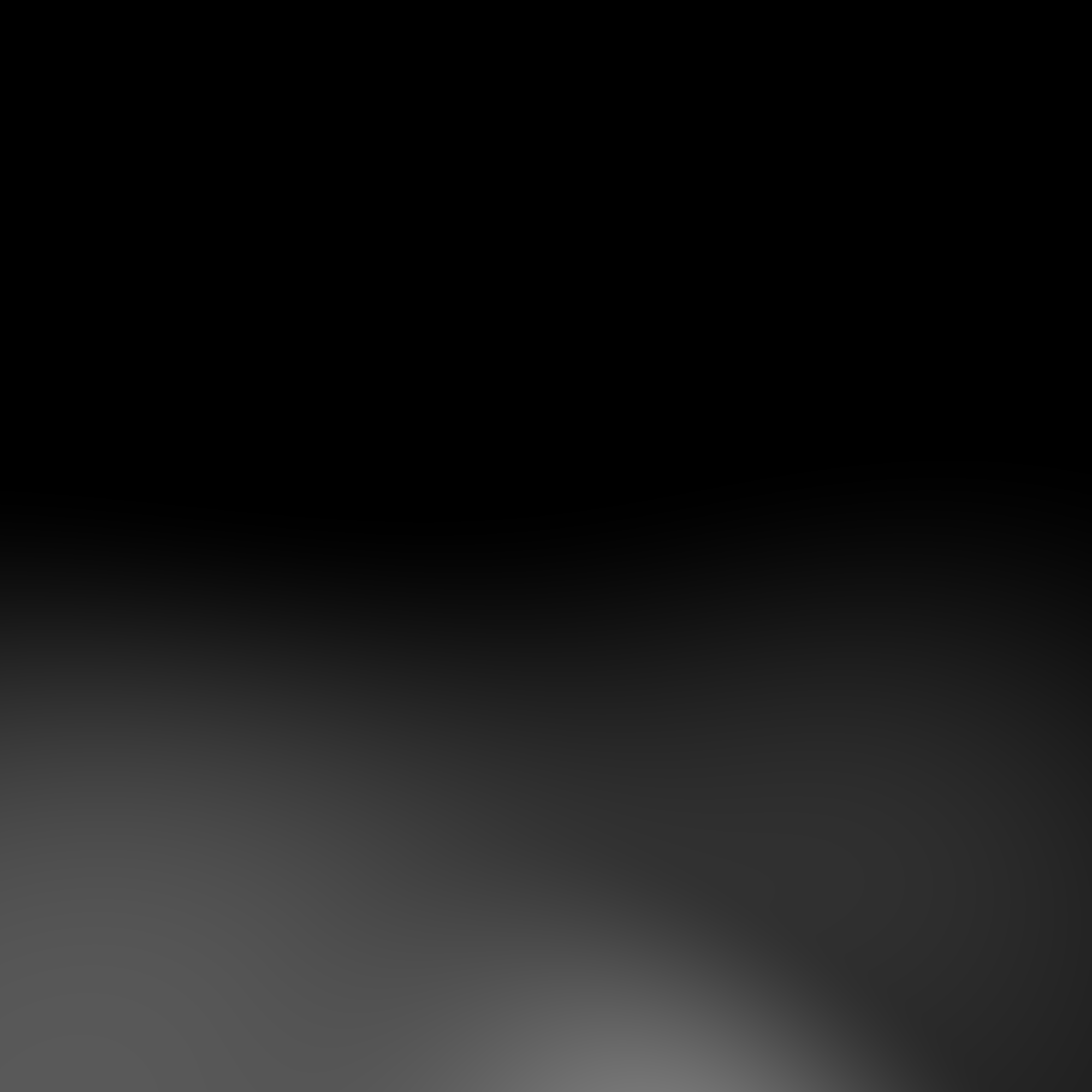
APICAL A1-CTFE Local Showers packages include:
Glassware
Centering Rings
Clamping Rings
Lattice Support for Bench-Top
Castered Skid for Kilo & Pilot
Lab Arms & Supports
Insulated Hoses
Stir Motor for Wiper Basket
2x Ejection Pump (heavies & solvent)
Injection Pump
Heater for Feed Tank & Lines
Heater for Main Body Jacket
Recirculator for Internal Condenser
Chiller for External Condenser
Diaphragm Valve
Vacuum Pump
Vacuum Control
Electric Cold Trap
Apical also provides:
Installation of Complete Systems
Training for Complete Systems
Installation Manual
SDS Sheets
SOP for Operation
On-Going Technical Support
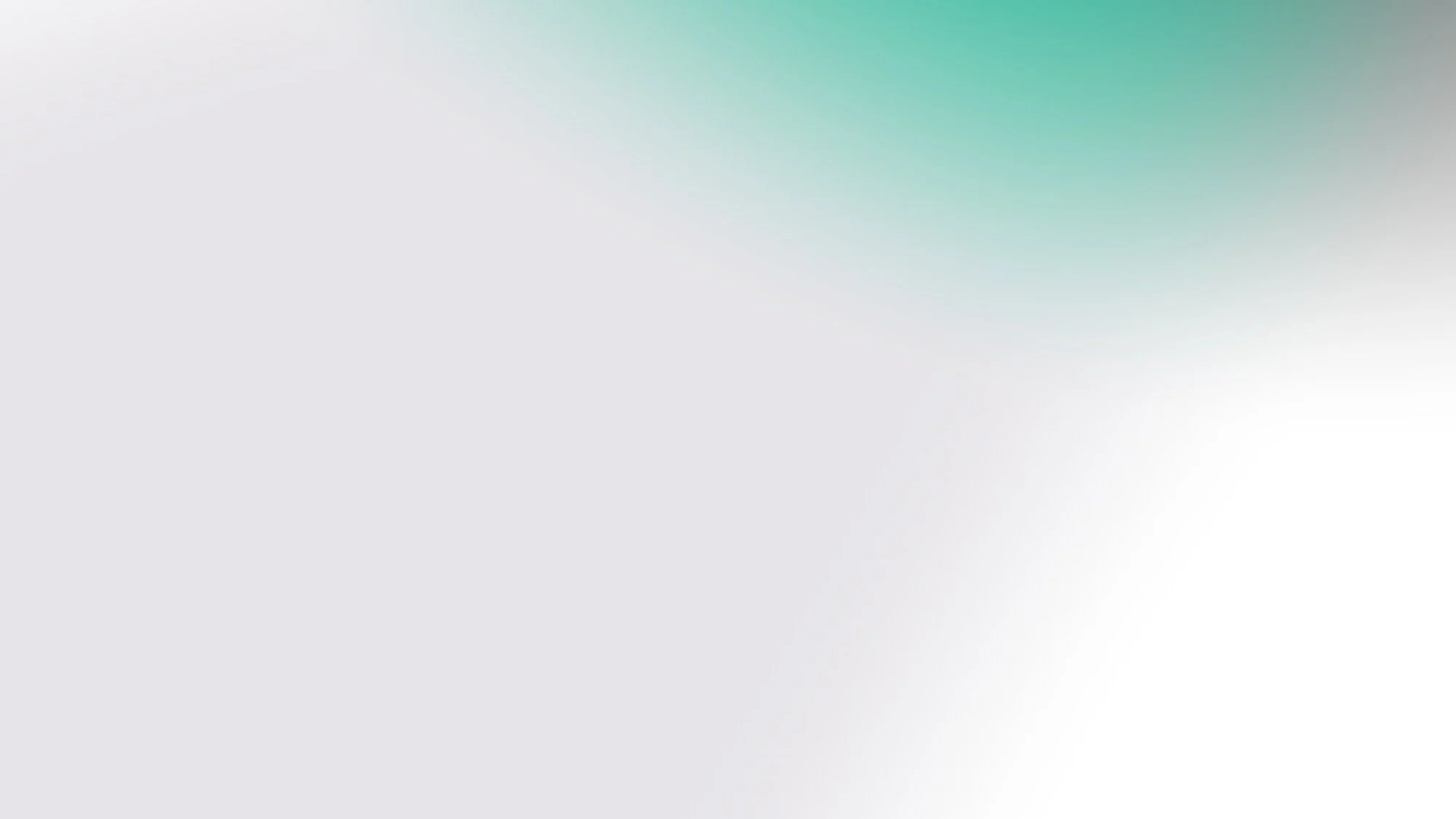
Continuous Systems Built for 24 Hour Operation
Main Body Distillation Rate
250mL to >200,000mL per Hour
Typical Start-up Time
30 Minutes
Typical Runtime
10 Hours
APICAL A1-CTFE Local Showers features:
-
Ensure leak-free fitment and ultimate vacuum potential for the system.
-
Grooved PTFE wipers ensure a consistently thin film for maximum evaporation and ultimate control of feed retention time.
-
Triple coil design with significant surface area fitted to handle the anticipated vapor load.
-
Captures light molecular compounds like terpenes and residual solvents while protecting the pump and reducing maintenance.
-
Retains heat & energy within the system to maximize efficiency while protecting from touch burns per OSHA standards and allowing the operator to see what is happening.
-
Reduces impedance on vapor path which improves vacuum depth and overall throughput.
-
Tubing where hot liquid can potentially pass or collect is vacuum insulated to prevent touch burns.
-
Fitted for deep-vacuum, durability and easy assembly/disassembly, these junctures are fitted with PTFE centering rings & composite clamps.
-
Principle glassware is meant to be permanently installed on the lattice to limit operator interaction.
-
Reflux of common solvents keeps systems looking and performing brand new for years to come.
-
Minority distillates collected on external condensers are sent to batch flasks that can be separated from the system during production.
-
Loaded solvent is pre-heated and metered into the system to ensure the highest and most consistent distillation rates.
-
Recovered solvents can be continuously ejected from the system while in production.
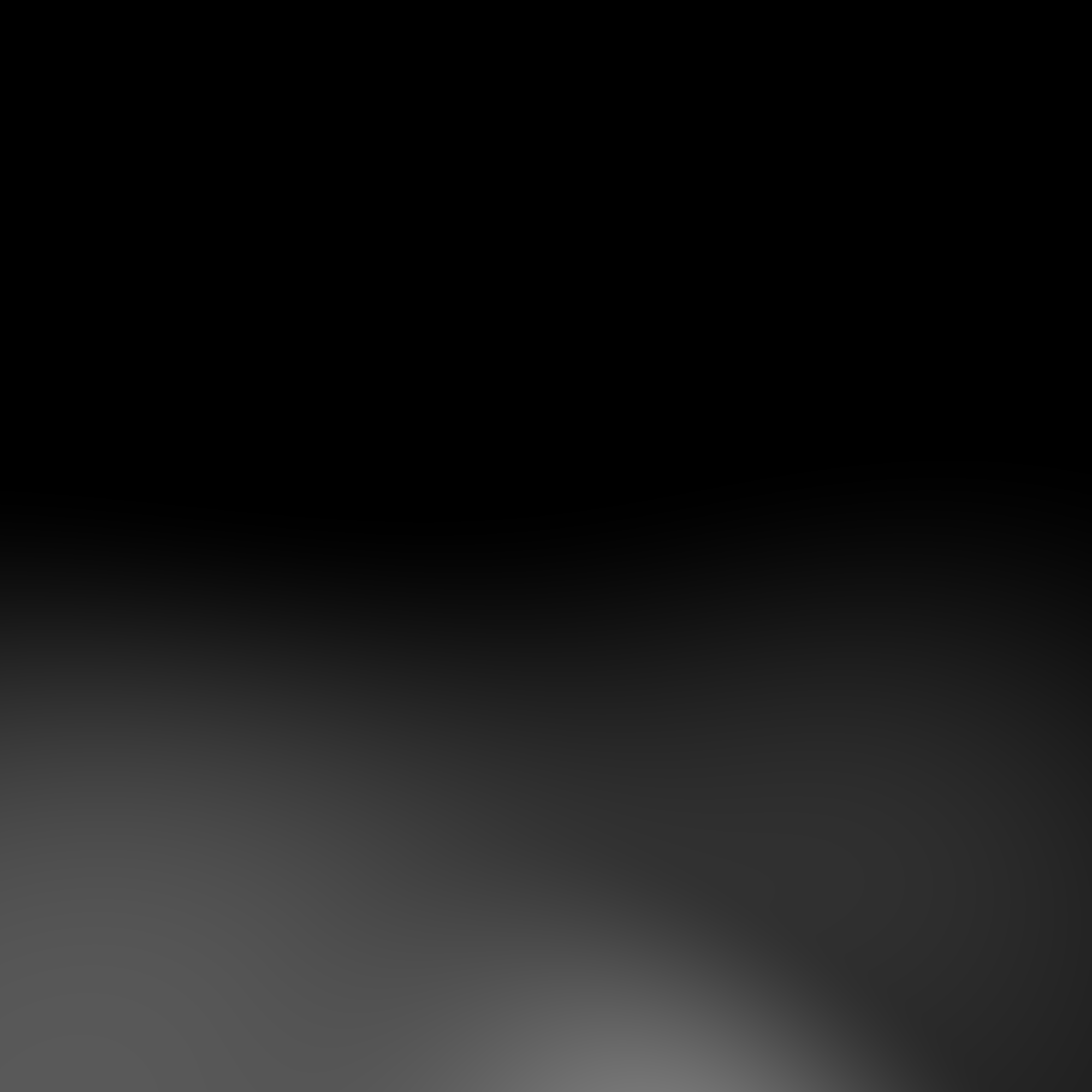