Reactor Work-Up & Distillations
Intended to perform bulk reactions, dissolutions and vacuum distillations through large diameter vapor ducts or complex, fractional distillation columns. These systems are chemical industry workhorses for a wide range of processes.
With Apical reactor solutions, operators enjoy precise control, compatibility and high throughput while owners rely on the durability, product consistency and protection against contamination Apical systems can offer.
Jacketed reactors range in size from 300mL to 200L, typically with a 10% minimum batch volume, offering a wide range of batch sizes, product yields & distillation rates. Apical has the flexibility to fit systems to your scenario without compromise.
And, our systems are built to meet explicit manufacturing guidelines set out by ASME, NEC, cGMP, OSHA and so forth. Apical ensures the safety of your operators with insulation, pressure relief, warning labels, shielding, PPE and training.
Apical has taken years of validated field experience and product trials to develop practical technologies that work every day. We combine academic principles with cutting-edge design to provide equipment that can be relied on for years to come with safe, easy operation, high throughputs and consistent product.
These reactor systems utilize large tubing to ensure an unimpeded vapor path which is critical to maintaining deep vacuum at the process rather than just at the pump. On the flip-side, PRVs and/or rupture discs are often fitted to lids and overhead assemblies to protect the staff and system components from overpressurization.
And, when scaling the ancillary glassware, motors, temperature control and pumps to fit, Apical works with trusted manufacturing partners known for their robust support staff and resilient equipment.
Considering these finer points is one of the keys to high throughputs, successful process development, facility safety and efficient commercialization.
With Apical, there are no myths about residence time, degradation or physics, no designs with built-in obsolescence, no exaggerations about system capabilities or pay-to-play obstacles to efficient processing.
Apical has tested a wide range of designs under production settings to pierce the veil and remove the mystique around commercial product development so business operators can focus on the customer.
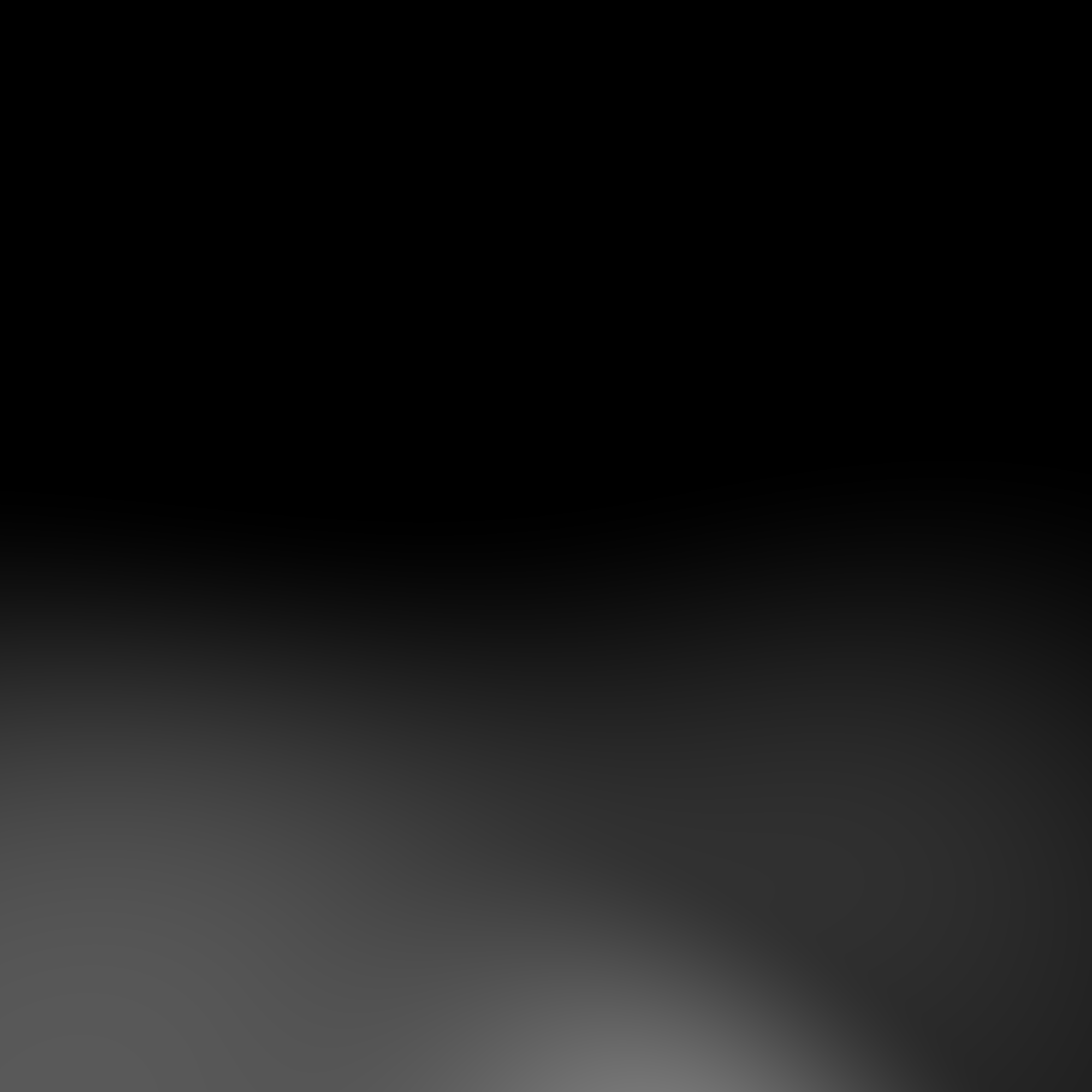
Apical Jacketed Reactor packages can include:
Glassware/Lined/Alloy Vessel & Lid
Distillation Overhead & Receiving Components
Stir Motor
PTFE, Hastelloy, etc. Stir Prop
Injection & Ejection Gear Pumps
Heater for Feed Tank & Lines
Recirculator for Jacket
Chiller for External Condenser
Diaphragm Valve
Vacuum Pump
Vacuum Control
Electric Cold Trap
Closed Solids Addition
Pressure Relief
Liquid Temperature & Level Monitoring
Centering & Clamping Rings
Lattice Support for Bench-Top
Castered Skid for Kilo & Pilot
Lab Arms & Supports
Insulated Hoses
Apical also can provide:
Installation of Complete Systems
Safety Training
Installation Manual
Materials Testing Portfolio & SDS
SOP for Operation
On-Going Technical Support
Process Review
Customization
Re-Lining
Apical reactors feature:
-
Ensure leak-free fitment and ultimate vacuum potential for the system.
-
Triple-coil, high surface area system supported by a high-flow chiller.
-
Retains heat & energy within the system to maximize efficiency while protecting from touch burns per OSHA standards and allowing the operator to see what is happening.
-
Turbulent, high-flow paths evenly distribute energy from incoming heat transfer fluid, preventing hot spots and speeding up time-to-temperature.
-
Reduces impedance on vapor path which improves vacuum depth and overall throughput.
-
Tubing where hot liquid can potentially pass or collect is vacuum insulated to prevent touch burns.
-
Fitted for deep-vacuum, durability and easy assembly/disassembly, these junctures are fitted with PTFE centering rings & composite clamps.
-
Principle glassware is meant to be permanently installed on the lattice to limit operator interaction.
-
Reflux of common solvents keeps systems looking and performing brand new for years to come.
-
Minority distillates collected on external condensers are sent to batch flasks that can be separated from the system during production.
-
Reagents, crude oils and solvents can be individually injected into the system with waste/reticulate and distillates being ejected.
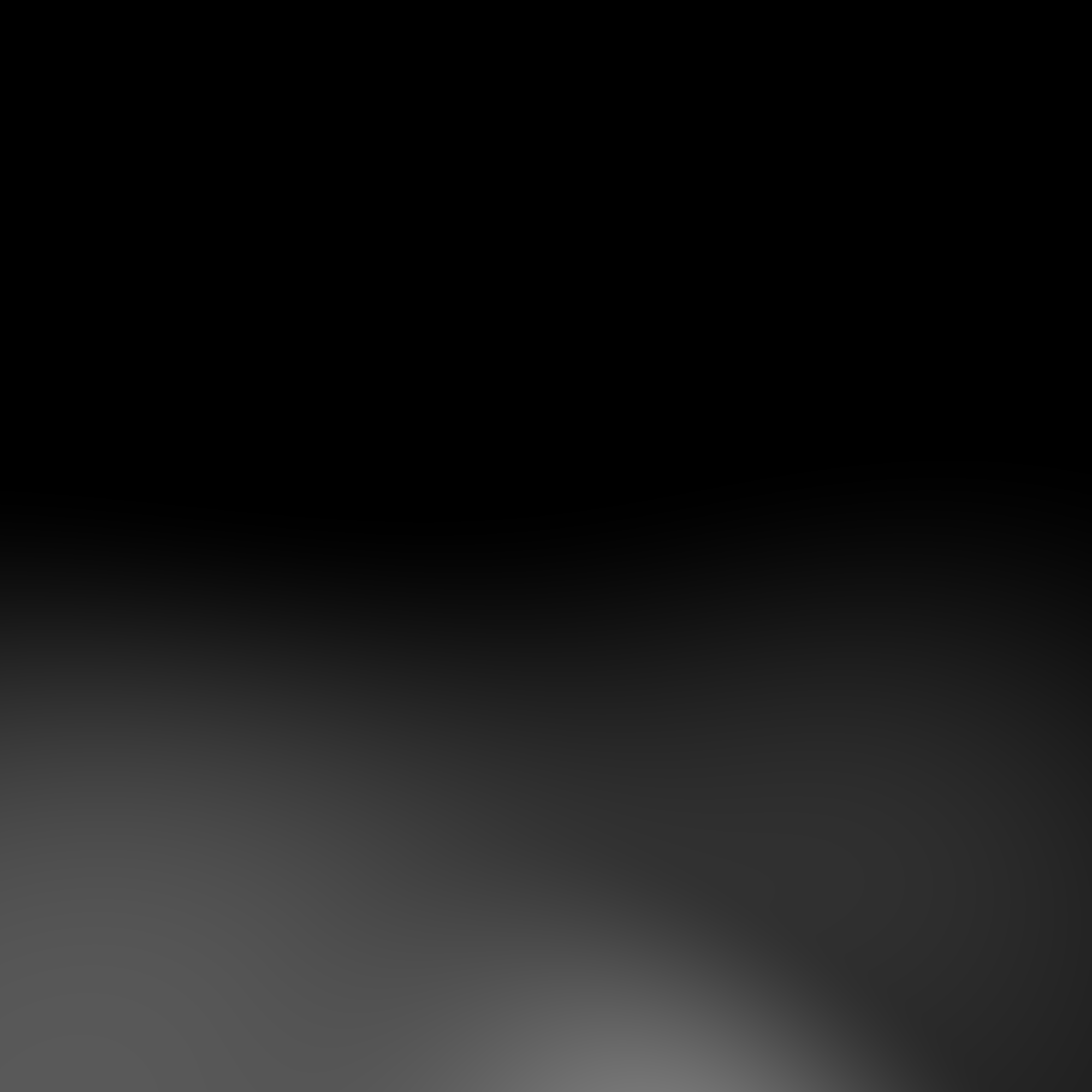