
GLASS REACTORS
A1-RDX Hurricane Series
Jacketed reactors are intended to perform scale-up and production of bulk reactions, isolations and distillations. The APICAL A1-RDX Hurricane Jacketed Reactor series offers reliable operation for work-up, slurry development, vacuum separations, synthesis and liquid extractions. These systems are chemical industry workhorses for just about any laboratory or commercial chemical facility.
Jacketed reactors paired with fractional columns (A1-RDX-FC) guarantee purities exceeding 90%, separating low, heavy and near molecular weight compounds. When fitted with a short vapor path (A1-RDX-SPE) and high surface area coil & plate condensers, these same reactors recover bulk solvent.
The right configuration exists for just about every chemical process. Apical delivers the correct assemblies for a wide range of operations:
synthesis
oxidation
crystallization
reflux
bio-reactions
halogenation
nitration
isomerization
Apical has taken years of validated field experience and product trials to develop practical technologies that work every day. We combine academic principles with cutting-edge design to provide equipment that can be relied on for years to come with safe, easy operation, high throughputs and consistent product.
These reactor systems utilize large tubing to ensure an unimpeded vapor path which is critical to maintaining deep vacuum at the process rather than just at the pump. On the flip-side, PRVs and/or rupture discs are often fitted to lids and overhead assemblies to protect the staff and system components from overpressurization.
Apical reactors have scale-up in mind, maintaining consistent ratios of dimension as they grow to ensure a reliable transition to larger processing. And, when scaling the ancillary systems, Apical works with trusted manufacturing partners known for their robust support staff and resilient equipment.
Considering these finer points is one of the keys to high throughputs, successful process development, facility safety and efficient commercialization.
Systems are built to DIN and cGMP standards for consistent production as well OSHA guidelines for safety. Apical takes industry guidelines seriously to ensure limited downtime, straight-forward audits and predictable operation.
The APICAL A1-RDX Hurricane series has a wide range of jacketed reactor configurations with our unique design features and efficiency-minded details differentiating our systems in a crowded marketplace.
The attributes of Apical jacketed reactors pair well with Schott glass ranging in sizes from 300mL to 150L.
With that, Apical has the flexibility to fit systems to your scenario without compromise.
hydrogenation
esterification
aging
decarboxylation
Apical has tested a wide range of designs under production settings to pierce the veil and remove the mystique around chemical processing so business operators can focus on the customer and not a daily headache.
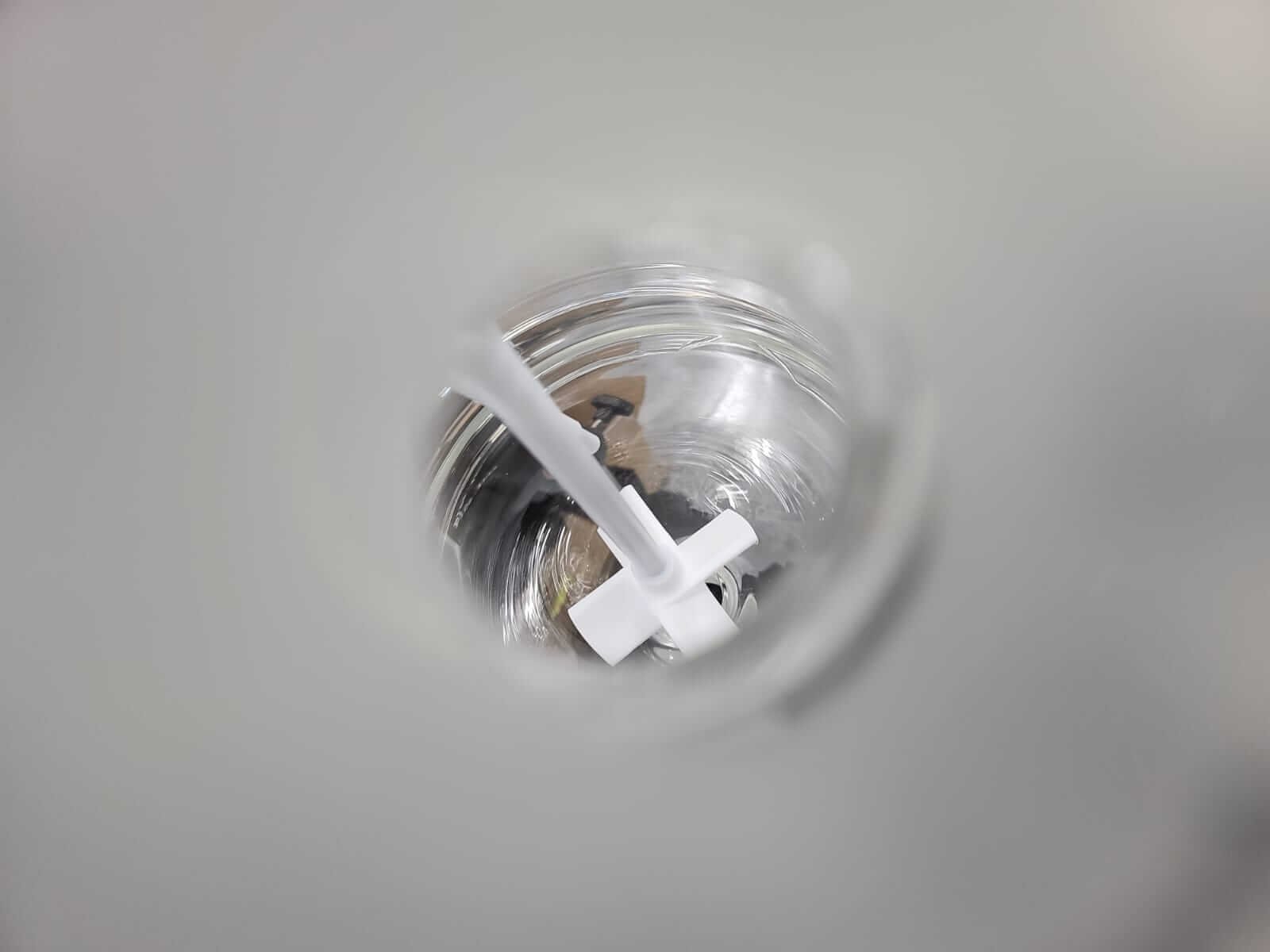
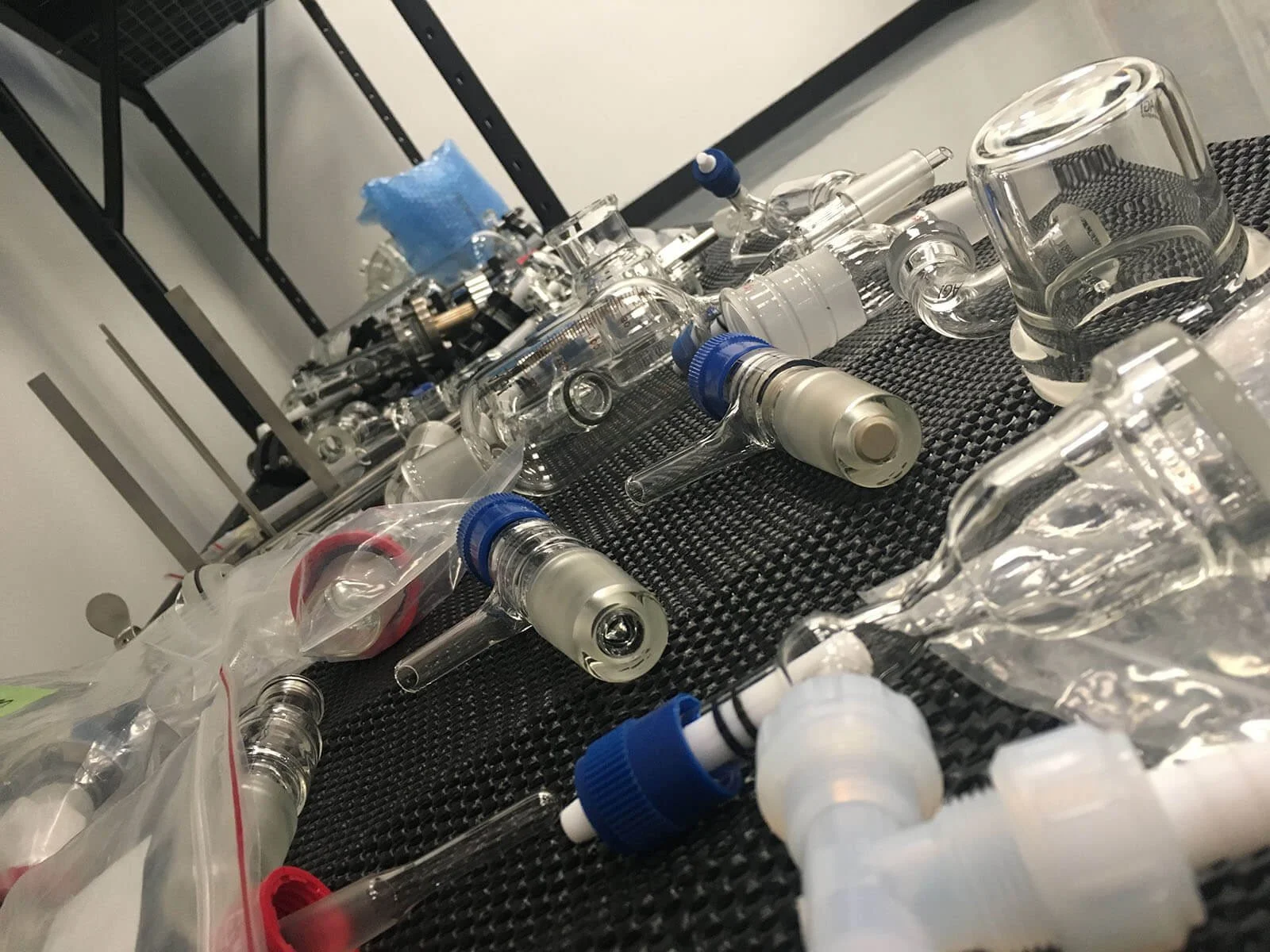

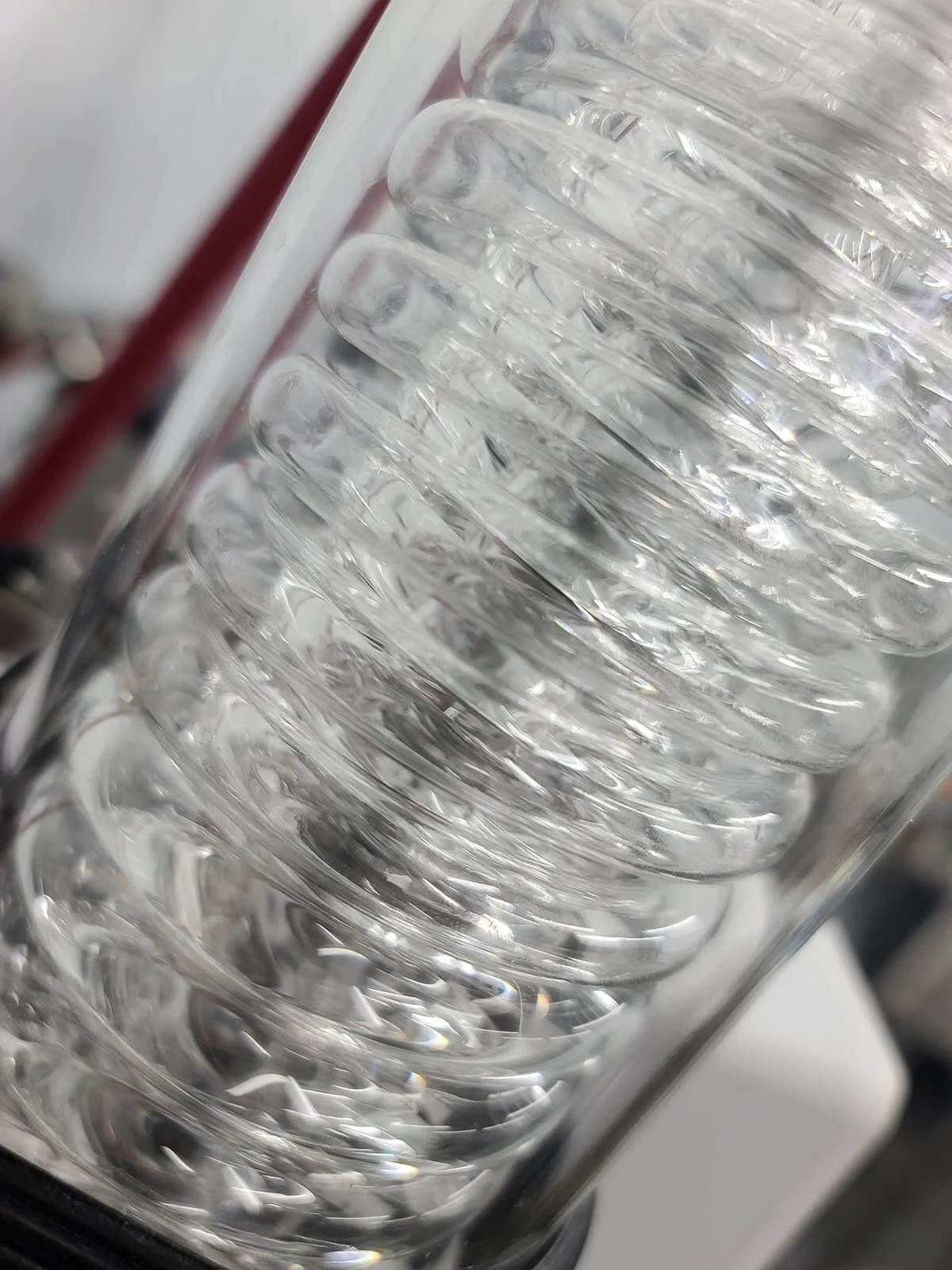
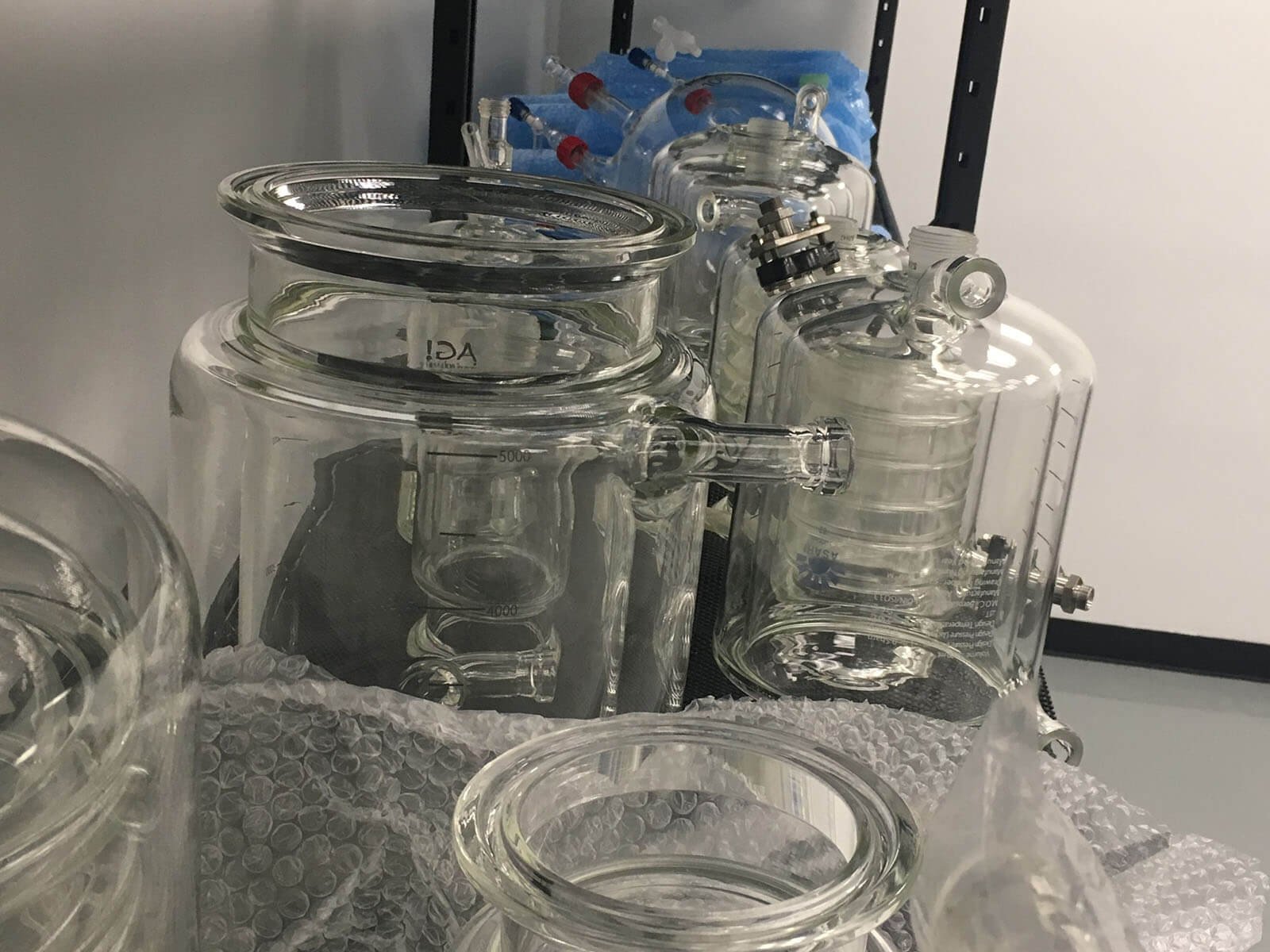
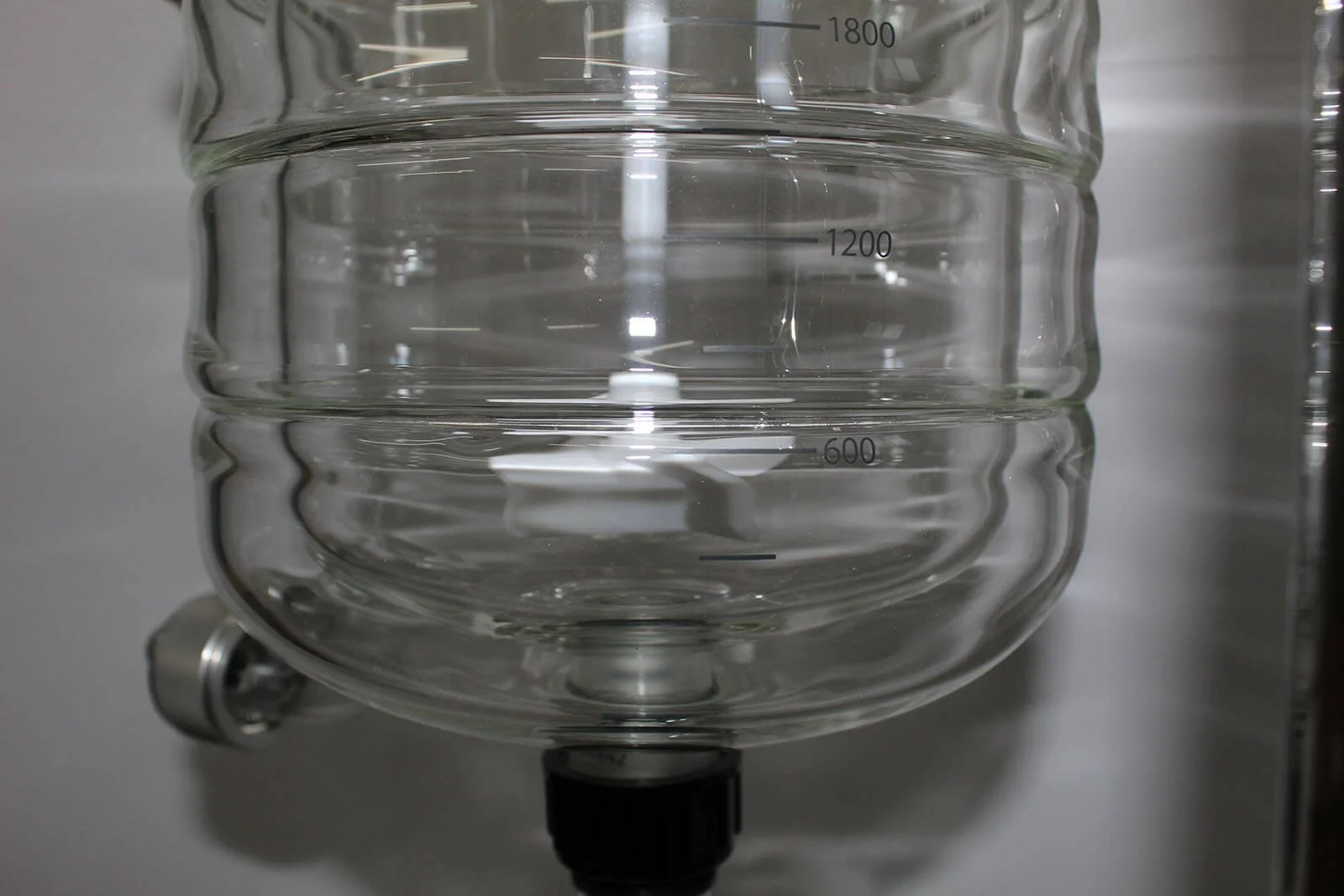
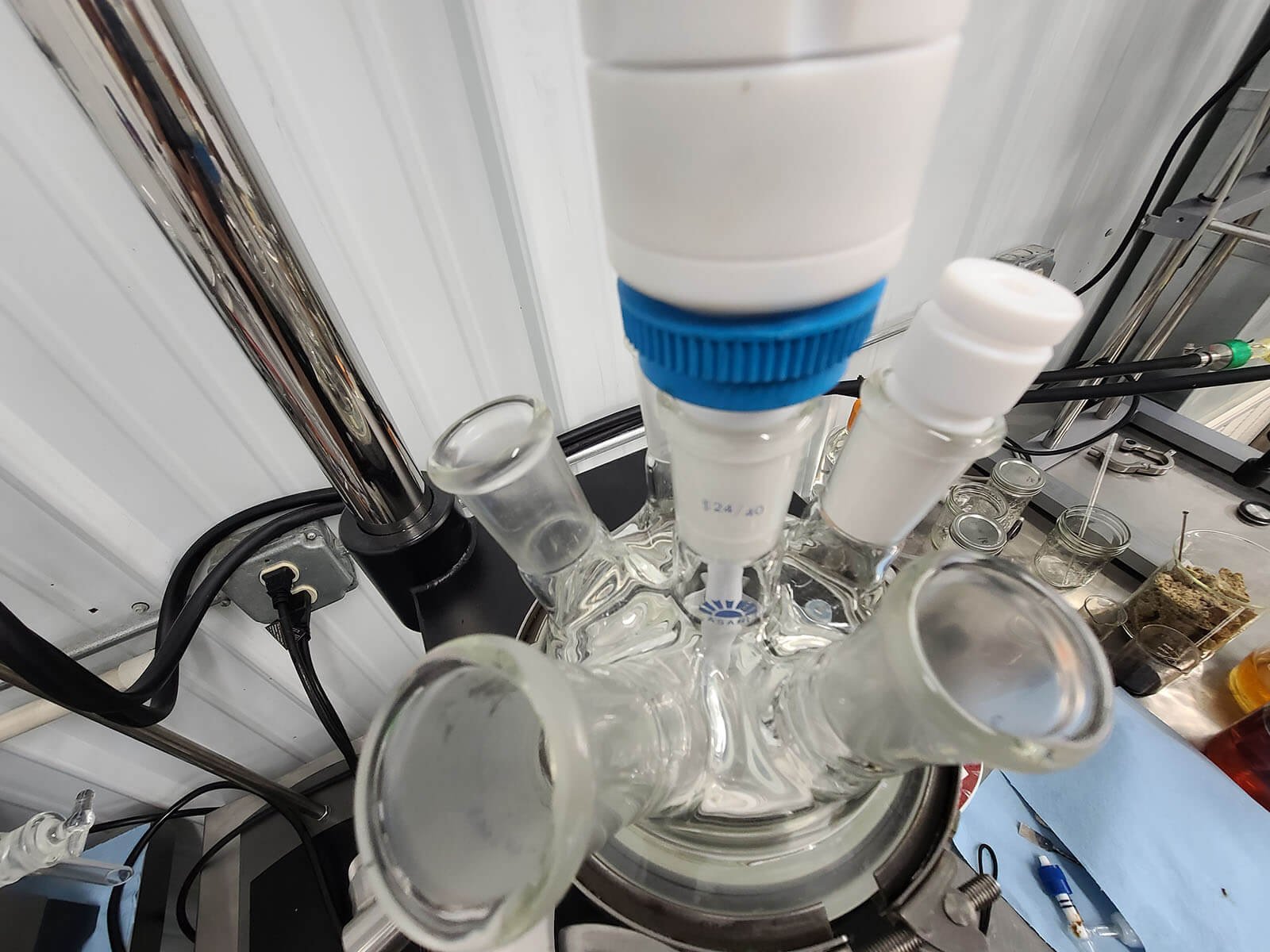
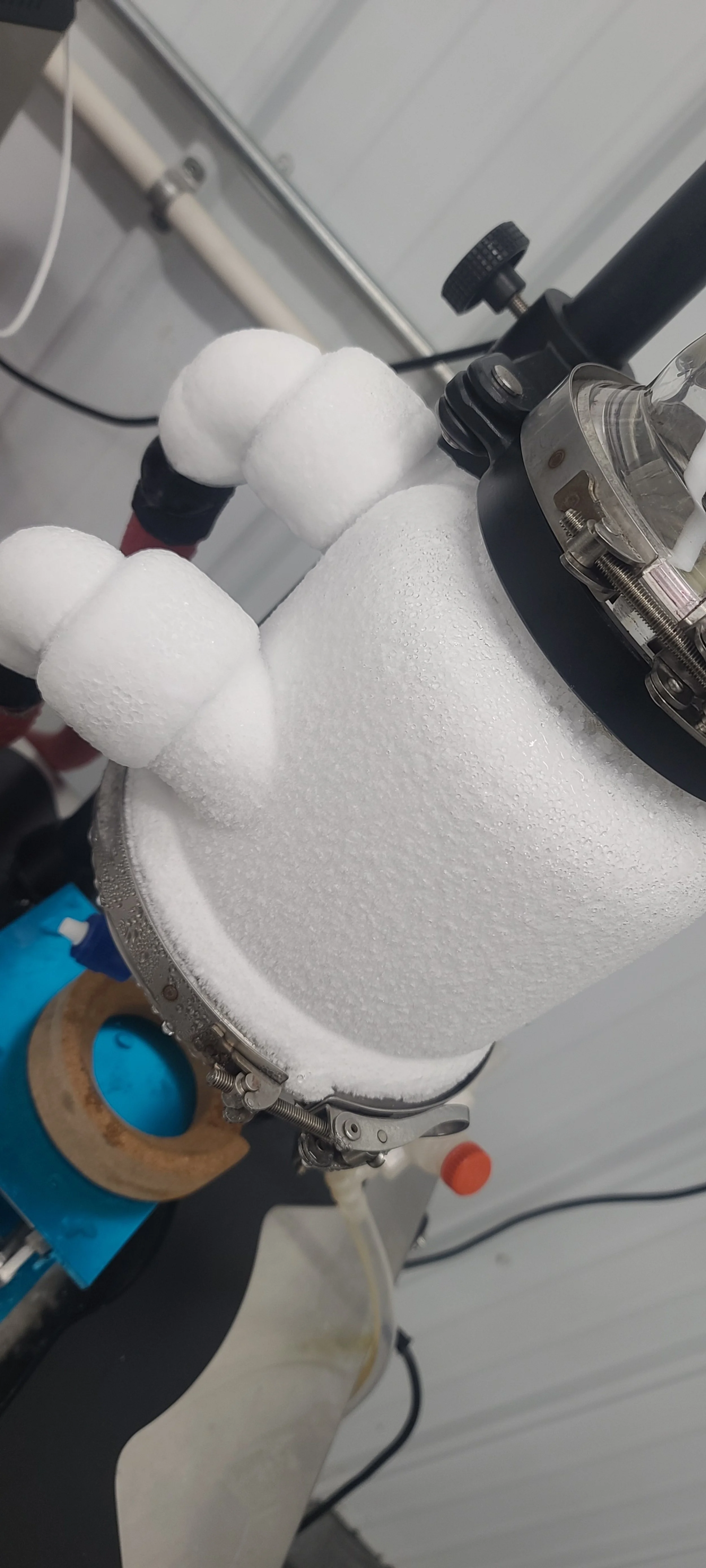

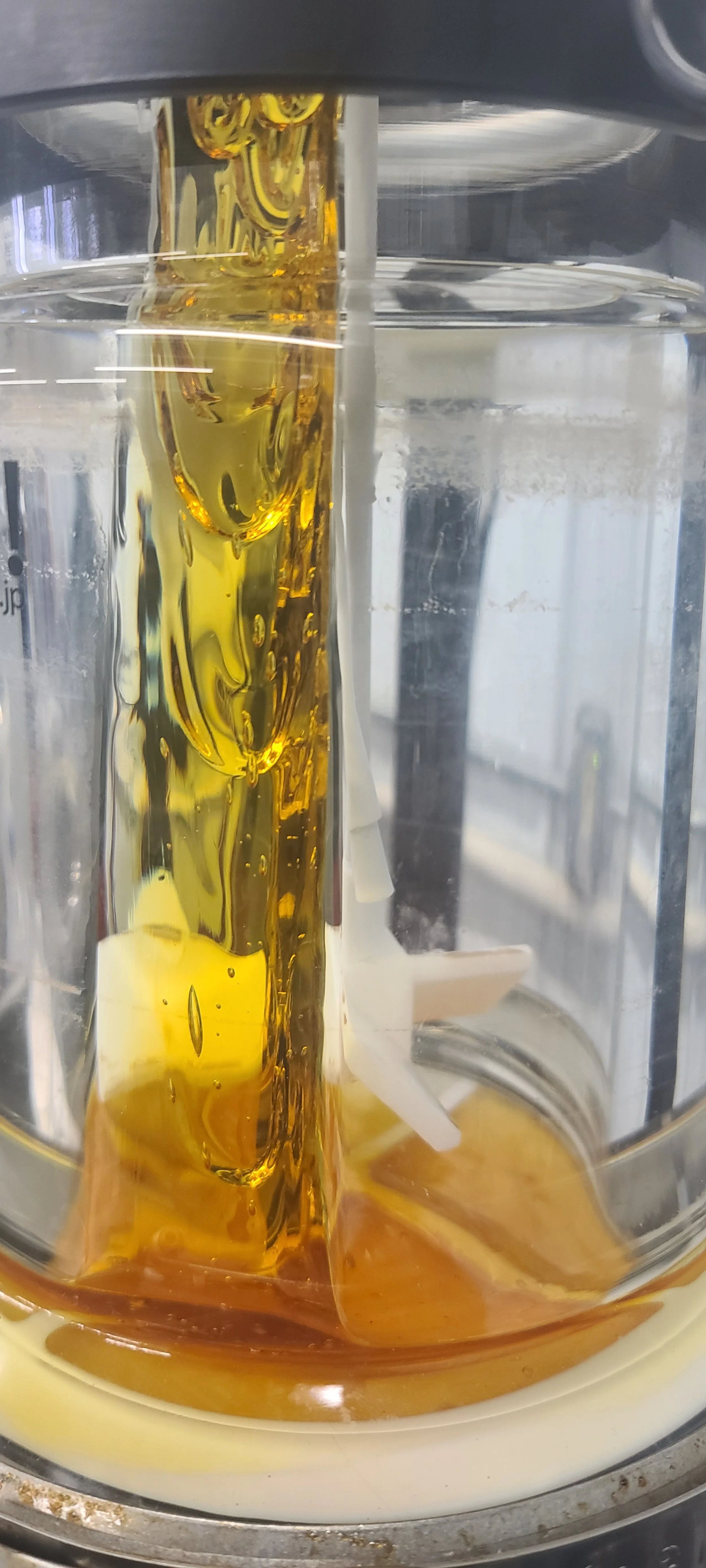


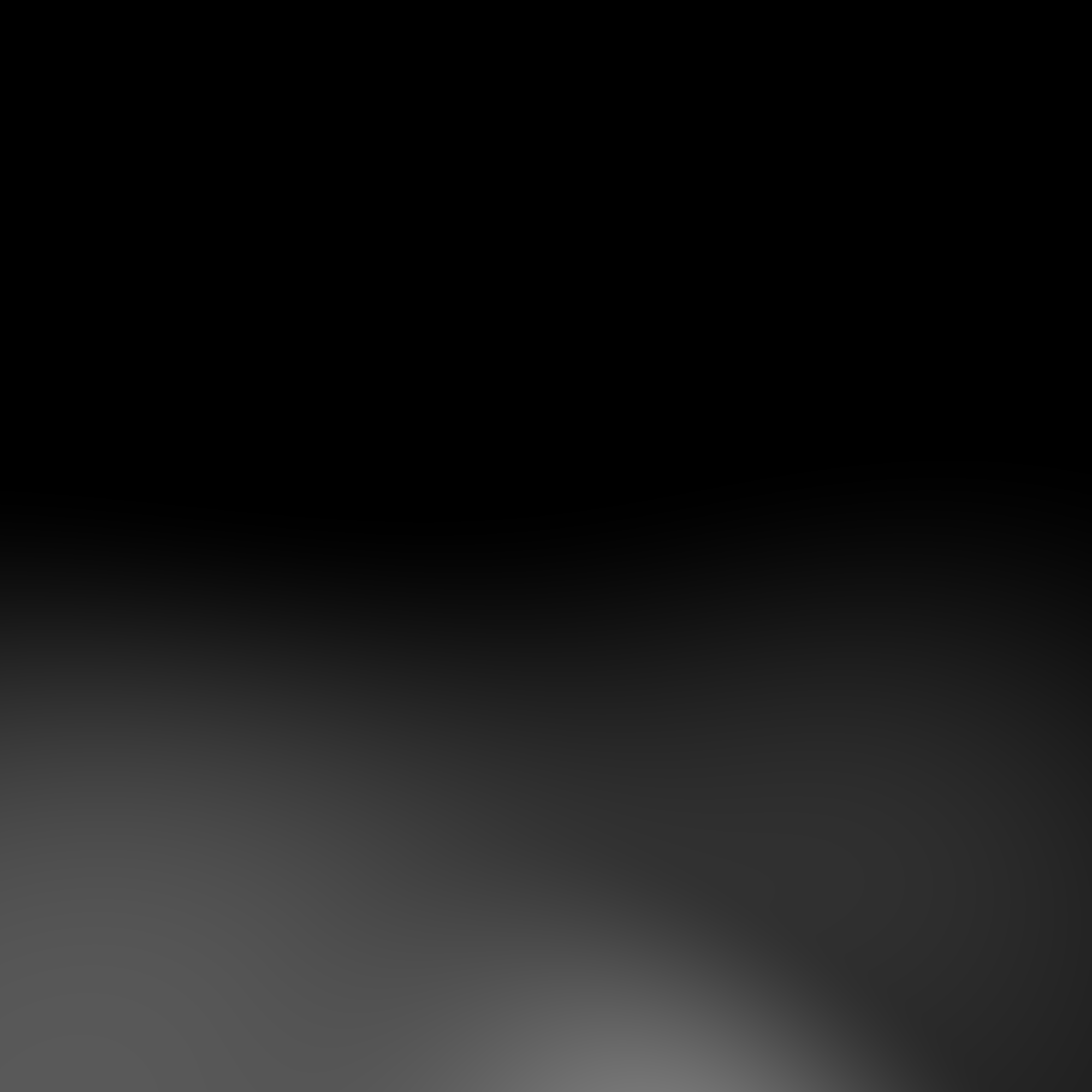
The A1-RDX Hurricane package can include:
Glassware/Lined/Alloy Vessel & Lid
Distillation Overhead & Receiving Components
Stir Motor
PTFE, Hastelloy etc. Stir Prop
Injection & Ejection Gear Pumps
Heater for Feed Tank & Lines
Recirculator for Jacket
Liquid Temperature & Level Monitoring
Centering & Clamping Rings
Lattice Support for Bench-Top
Castered Skid for Kilo & Pilot
Lab Arms & Supports
Insulated Hoses
Etc.
Chiller for External Condenser
Diaphragm Valve
Vacuum Pump
Vacuum Control
Electric Cold Trap
Closed Solids Addition
Pressure Relief
Apical also provides:
Installation of Complete Systems
Training for Complete Systems
SOP for Operation
On-Going Technical Support
Installation Manual
SDS Sheets
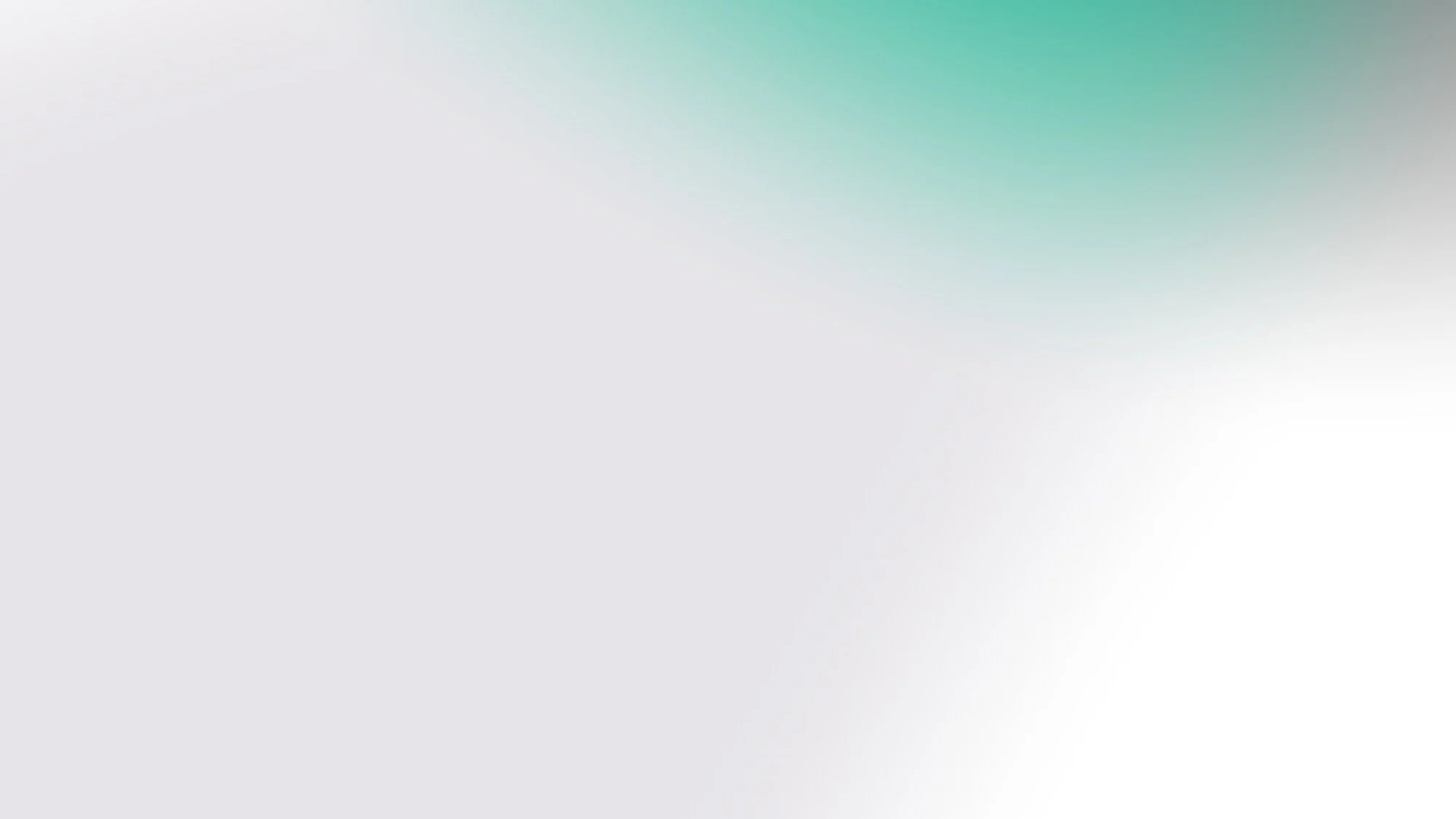
Optimized Capacity
80% Total Volume
Batch Capacity
300mL to 150,000mL
Typical Start-Up Time
30 Minutes
Typical Batch Runtime
3 to 24 Hours
A1-RDX Hurricane series features include:
-
Fully utilizes the power of vacuum, limiting the gradient between pump & process and improving consistency of performance.
-
Retains heat & energy within the system to maximize efficiency while protecting from touch burns per OSHA standards and allowing the operator to see what is happening.
-
Added turbulence increases efficiency of the recirculator, balances temperature throughout the condenser to improve condenser capacity and is vacuum-insulated to prevent touch burns.
-
Tubing where hot liquid can potentially pass or collect is vacuum insulated to prevent touch burns.
-
Fitted for deep-vacuum, durability and easy assembly/disassembly, these junctures are fitted with PTFE centering rings & composite clamps.
-
German-made components known for consistency and longevity.
-
Principle glassware is meant to be permanently installed on the lattice, frame or skid to reduce breakage and increase safety.
-
Reflux of common solvents keeps systems looking and performing brand new for years to come.
-
Small & large vessels and be fitted with lifting systems, allowing for easy cleaning, maintenance and swapping of process vessels.
-
Designed for bump & heavy molecular weight rejection, making for easier operation.
-
Distillates can be collected in batch flasks that can be separated from the system during production.
-
Waste, product & distillates can be continuously ejected from the system while in production.
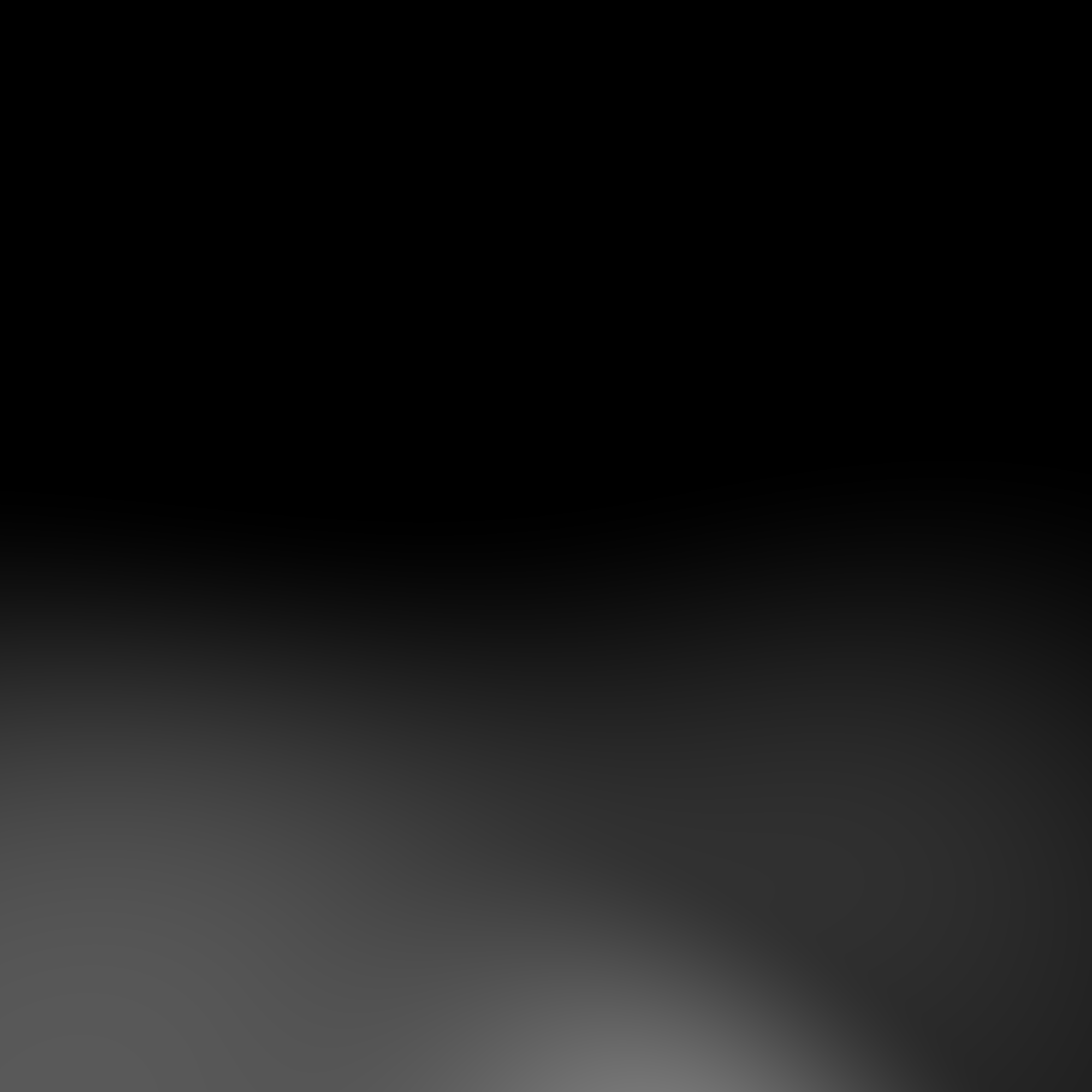