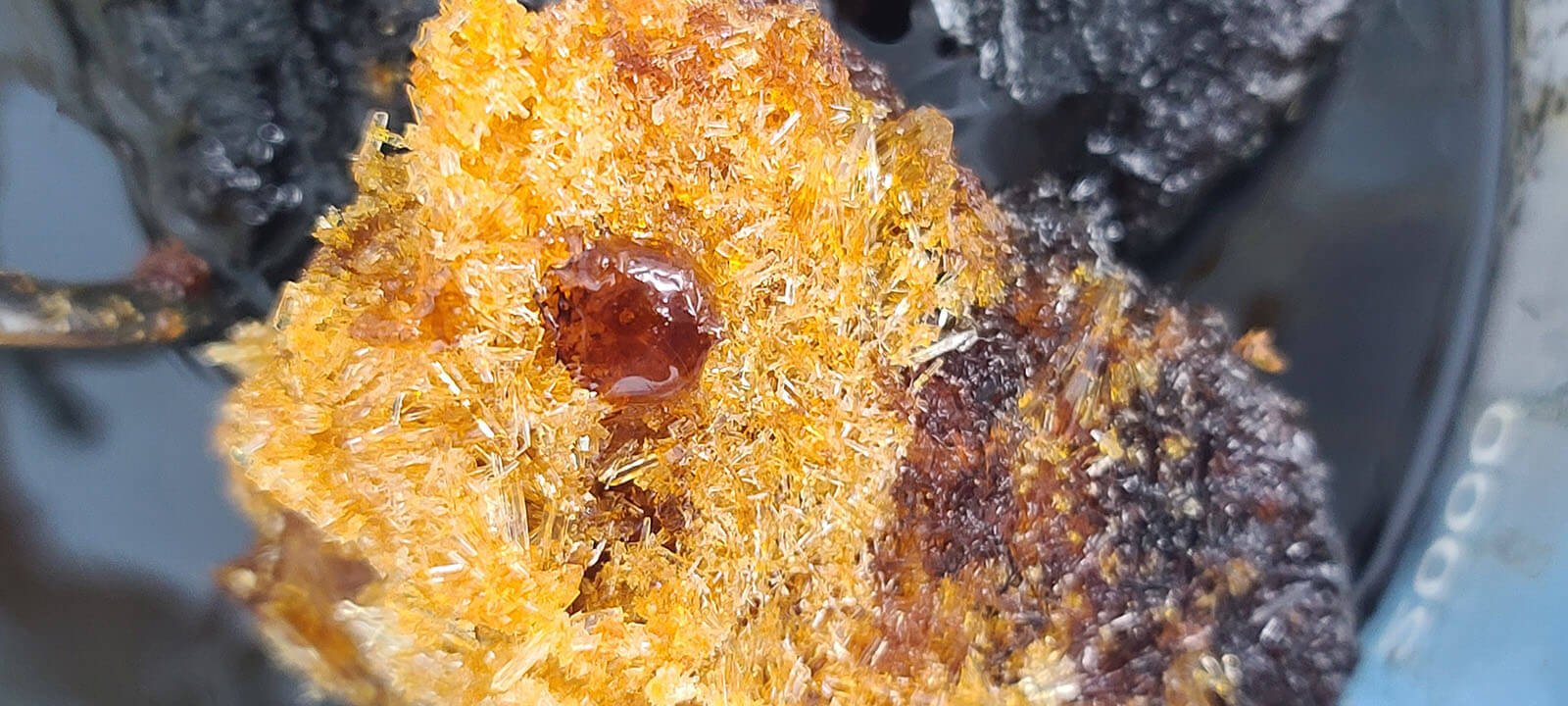
ASME Vessels, Reactors & Specialty Alloys
A1-INGOT Series
As the chemistry becomes larger, more complex, corrosive and demanding, Apical alloy jacketed reactor & tank solutions often play a critical role in reliable processing.
Apical has taken years of validated field experience and added further insight from our deep network of industry professionals. We combine academic principles with cutting-edge design to provide equipment that can be relied on for years to come with safe, easy operation, high throughputs and consistent product.
Choose the correct method of construction is critical in protecting processing equipment from corrosion across a wide range of conditions. Countless alloys have been developed to address the specific pitfalls of each industry when building equipment for long-term production and a good return on investment. These factors ensure equipment longevity, particularly when faced with strong acids under high pressures and temperatures. On the product side, a resilient alloy is preventing contamination when it resists corrosion and scavenging. These materials are critical to functioning in industries utilizing APIs, nuclear, hazardous and chemicals manufacturing.
Apical reactors have scale-up in mind, maintaining consistent ratios of dimension as they grow to ensure a reliable transition to larger processing. And, when scaling the ancillary systems, Apical works with trusted manufacturing partners known for their robust support staff and resilient equipment.
Considering these finer points is key to:
high throughputs
proper material selection
equipment lifespan
corrosion & stress analysis
process development
facility safety
efficient commercialization
Hastelloy (C-275, 22, 2000)
Inconel
Monel
Nickel
Systems are built to DIN and cGMP standards for consistent production as well OSHA guidelines for safety. Apical takes industry guidelines seriously to ensure limited downtime, straight-forward audits and predictable operation.
The APICAL A1-INGOT series has a wide range of jacketed reactor & tank configurations with our unique design features and efficiency-minded details differentiating our systems in a crowded marketplace.
Depending on the required materials, design and specifications, Apical vessels can range from 50L to over 100,000L.
With that, Apical has the flexibility to fit systems to your scenario without compromise.
Mild Steel
Stainless Steel
Duplex
Tantalum
Apical has tested a wide range of designs under production settings to pierce the veil and remove the mystique around chemical processing so business operators can focus on the customer and not a daily headache.
Titanium
Alloy 20
Alloy 400
Zirconium
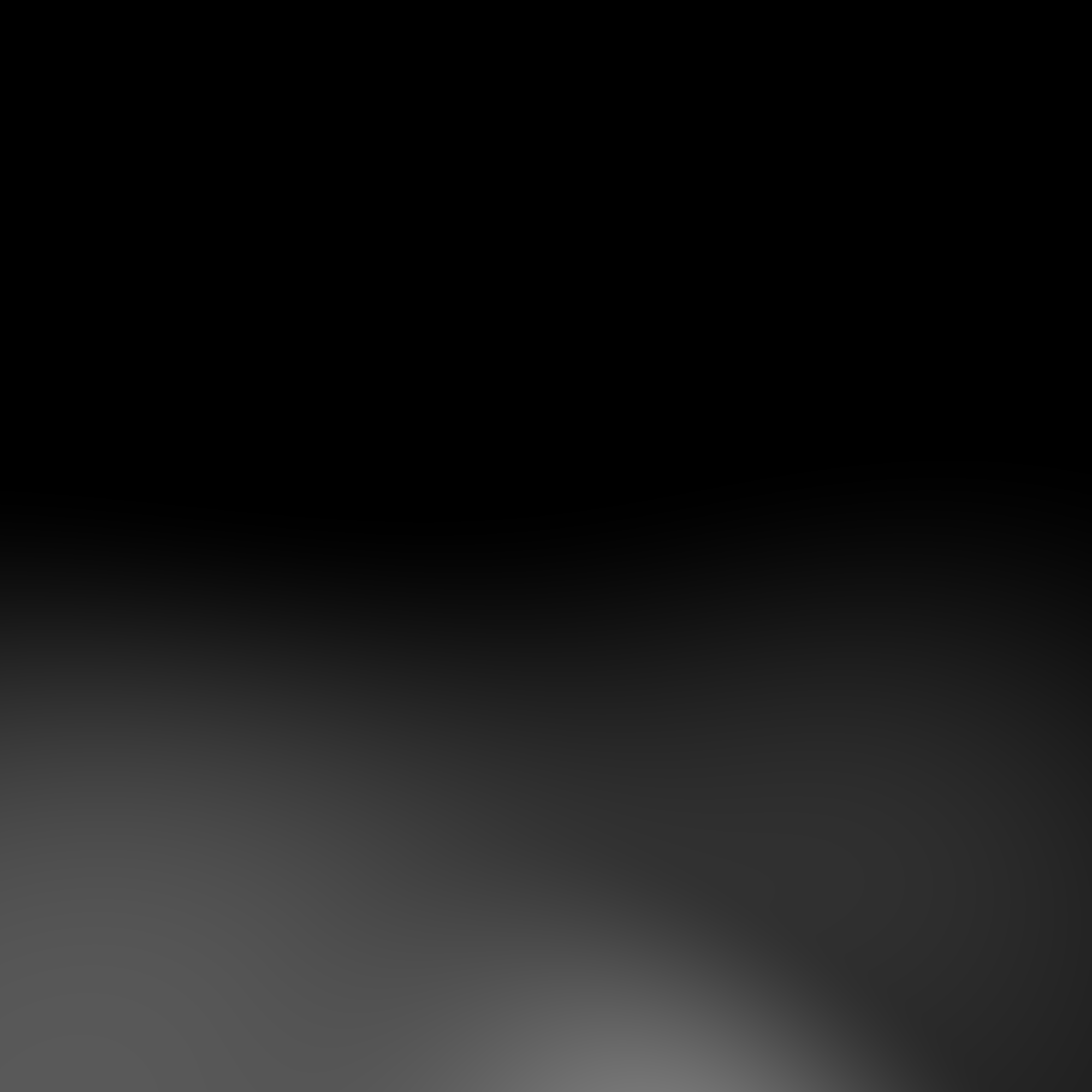
The A1-Ingot series covers:
Condensers
Nutsche Filter Reactors
Baffles
Stir Props
Reactive Heat Exchangers
Pressurized Filters
Condensers
Distillation Columns
Rainwater Collection
Sanitary Storage
& more.
Storage Vessels
Ultra-High Purity Tanks & Components
Liquid & Gas Heat Exchangers
Jacketed Steel Reactors
Apical also provides:
Installation of Complete Systems
Training for Complete Systems
Installation Manual
SDS Sheets
SOP for Operation
On-Going Technical Support
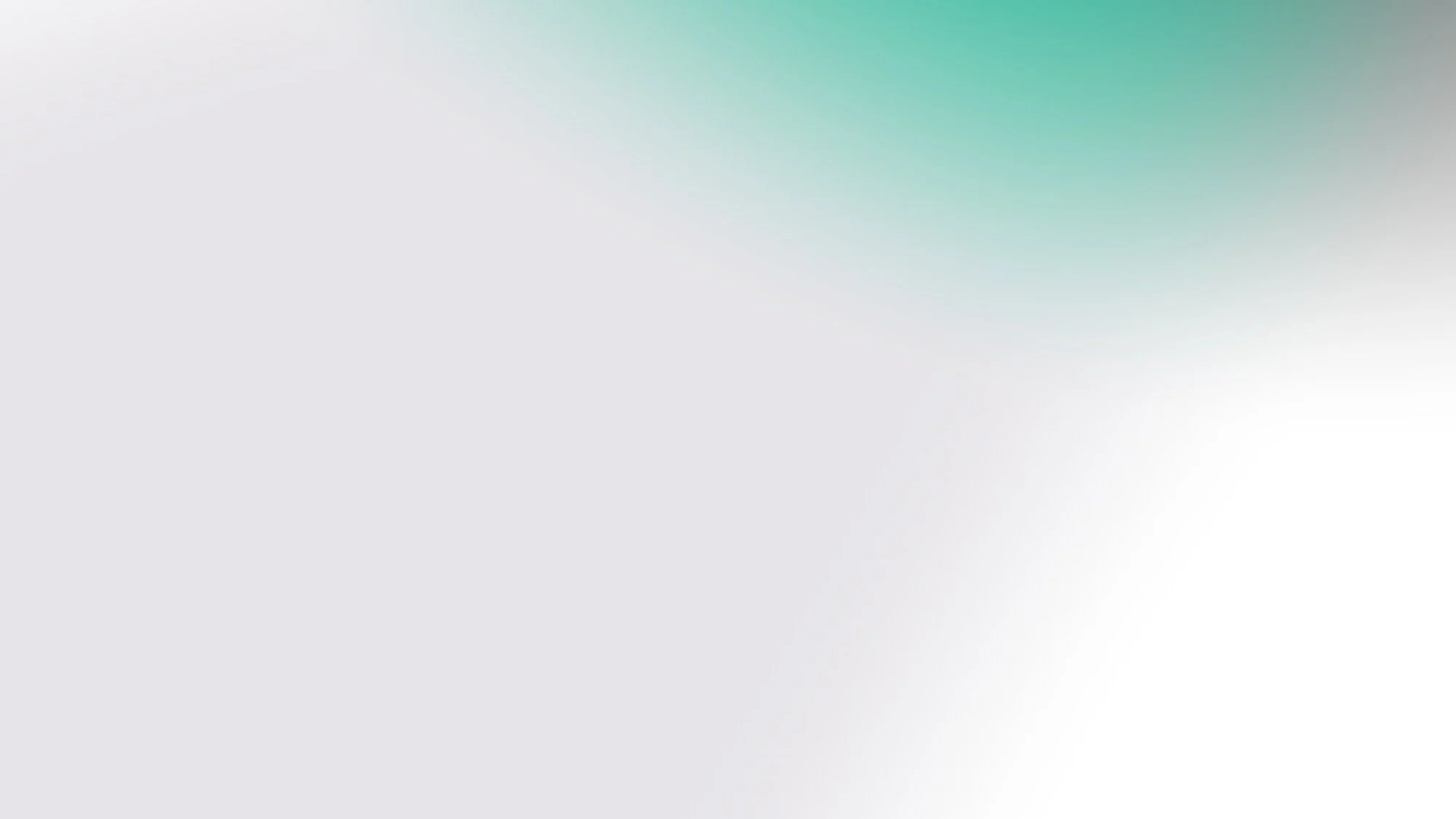
Batch Capacity
100mL to >100,000L
Optimized Capacity
80% Total Volume
Typical Start-up Time
30 Minutes
Temperatures
-75°C to 260°C
Vacuum/Pressure
FV to >30bar
Typical Batch Runtime
3 to 24 Hours
A1-Ingot series features include:
Built to DIN 28018, DIN 28136, DIN 28007 & ASME VII Div. 1 standards.
Mild Steel, Stainless Steel, Hastelloy® C-276, C-22 & C-2000,
Inconel, Monel, Nickel, Titanium, Alloy 20 and more.
-
Fitted for the specific process whether distillation, suspension, dissolution, crystallization etc.
-
Baffled or coiled jackets for superb temperature control.
-
Mirror/matte finishing, insulation, cladding, SIP/CIP, easy access/cleaning, etc.
-
Fitted for deep-vacuum, durability and easy assembly/disassembly, these junctures are fitted with PTFE centering rings & composite clamps.
-
German-made components known for consistency and longevity.
-
Principal vessels are meant to be permanently installed on the lattice, frame or skid to reduce breakage and increase safety.
-
Reflux of common solvents keeps systems looking and performing brand new for years to come.
-
Small & large vessels and be fitted with lifting systems, allowing for easy cleaning, maintenance and swapping of process vessels.
-
Waste, product & distillates can be continuously ejected from the system while in production.
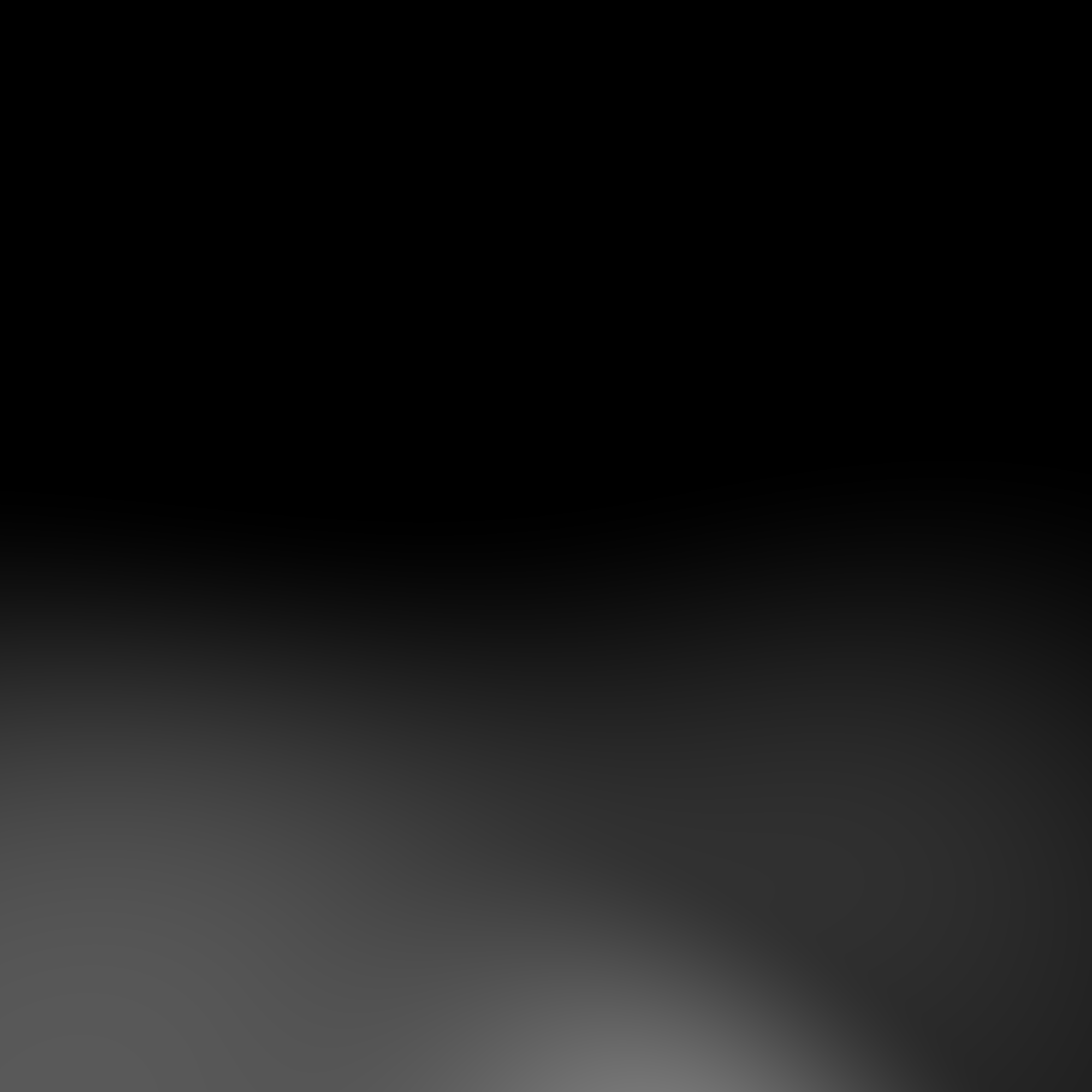
Systems are designed & built to DIN standards.
Glassware meets ASTM specifications and is sourced from Kimble Kimax or Schott Duran Glass.
Alloys are tested for ultra-high purity and corrosion resistance.
Design to meet ASME, ISO, AWS, DIN, etc.
Reactors, Filter-Dryers, Autoclaves, Heat Exchangers, Distillation Columns, Column Internals, ANFD, RVPD, etc.